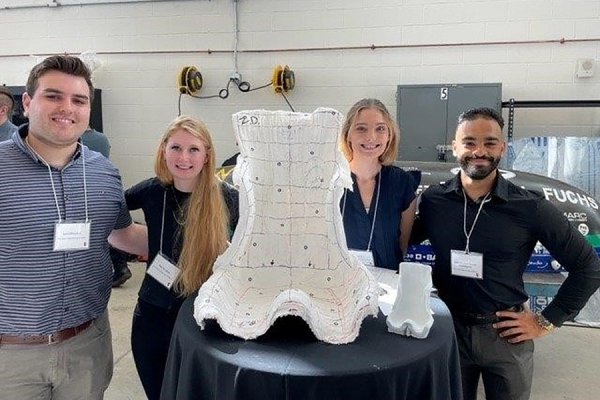
A manufacturing process developed with help from UWindsor engineering students can help children with special needs get a customized wheelchair faster.
The team, fourth-year engineering majors Luka Mlinarevic, Pavneet Sarao, Alea Mclellan, Jasmine Bull, and Saifaldin Abdelhamid under the direction of professor Colin Novak, has been working with the John McGivney Children’s Centre (JMCC) to speed up its production of specialized seats uniquely designed to meet the specific needs of each child.
The high-quality individualized seats are better suited to young clients than those procured off the shelf, explained team member Bull.
“These custom-moulded seats make a huge difference for these children by providing optimal alignment and support while improving their well-being,” she said.
The new process, presented during the Faculty of Engineering Design Demo Day on July 29, has the potential to reduce production time to three or four weeks rather than the current six to eight months. It will introduce innovative technologies with support from Harbour Technologies, Valiant TMS, and other local partners.
“Our current approach was a mix of internal and external processes that could be costly and labour intensive at times, and the COVID-19 pandemic exacerbated those challenges, introducing unpredictability in the cost and delivery of materials” said JMCC seating technologist, Gerry Demers.
JMCC CEO Jessica Sartori expressed gratitude to the UWindsor team and its industry partners.
“We will be a centre of excellence for this process and are excited to share this best practice with the other 21 children’s treatment centres across the province,” she said.
Bull said she and her classmates valued the experience.
“Our capstone project allowed us the unique opportunity to step outside of our textbooks and into the community,” she said.