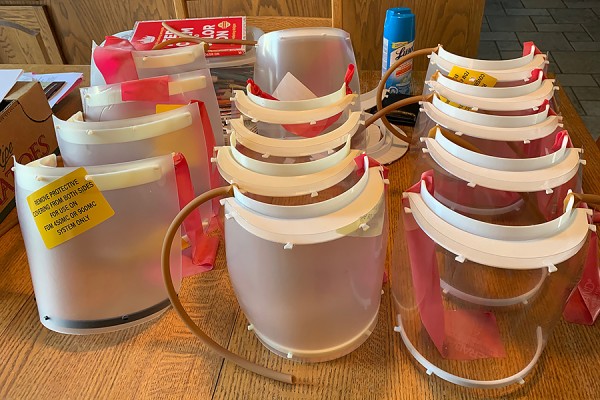
A local manufacturer has teamed with a group of researchers at UWindsor’s Faculty of Engineering to help combat the spread of COVID-19.
Valiant TMS is assisting professor Jill Urbanic’s research team with the production of brackets for 3D-printed face shields. The global company headquartered in Windsor has provided material, testing, building, and assembly support.
“We have no specific production targets. We are trying to meet requests and there have been several from a wide variety of front-line personnel,” Dr. Urbanic says. “This need is what is driving us forward.”
So far, shields have been delivered locally to three nursing departments at Windsor Regional Hospital, two nursing homes, and an x-ray clinic, and up Highway 401 to the intensive care unit at St. Joseph’s Hospital and St. Joseph’s Family Medical and Dental Centre in Toronto.
The shields are designed to be lightweight and adjustable in size. Urbanic says the designs have been optimized to leverage the most effective manufacturing processes.
“The top cover and retainer can be laser cut or water jet cut. The materials should allow for reuse. We would like to pursue molding the flexi-band with local mold shops, if they are interested.”
Master’s student Alireza Pasha and doctoral candidates Hamed Kalami and Morteza Alebooyeh have been brainstorming with Urbanic since the pandemic hit.
In addition, the team has designed hands-free openers for doors using a J-hook attachment so people can use their forearms to pull a door open. It works on doors with vertical bars for handles, but the team has designed versions for other types of door handles, too. The graduate students are also using the 3D printer to make prototypes of parts for ventilators.
“While there has been no recognized treatment for the virus to the moment, effective prevention with these high-demand supplies and tools is of the most importance,” Alebooyeh said.
Urbanic credits her students for putting their expertise and ingenuity to good use.
“All of us have been wanting to help,” she says. “This is our duty to society.”
Several departments university-wide have joined in on the effort, including UWindsor Print Shop’s Jen Almeida, who secured the plastic materials used for the visors. UWindsor EPICentre’s Wen Teoh, Amandeep Singh, and Paul Brereton are assisting with laser cutting the top cover and retainer and printing the flexi-band part. Rod Strickland and Michael Lucenkiw from the School of Creative Arts have also assisted with printing efforts.
“Quite frankly, nothing would have happened with respect to getting this from a lab environment to a test environment without Valiant’s help, in particular Glenn Strome, one of their project managers,” Urbanic says.
“CAMufacturing Solutions, Inc. has been involved in sourcing hand band straps, face shield materials, logistics, etc. and we also managed to get TheraBands from a local physiotherapist, Praveen Oommen from Sabga Physiotherapy-Huron (the CARE Institute) who provided materials when we didn’t receive our order on time.”
—Kristie Pearce
This article, an update to a DailyNews article written by Sarah Sacheli, was featured in the 2020 spring issue of the Windsor Engineering newsletter.