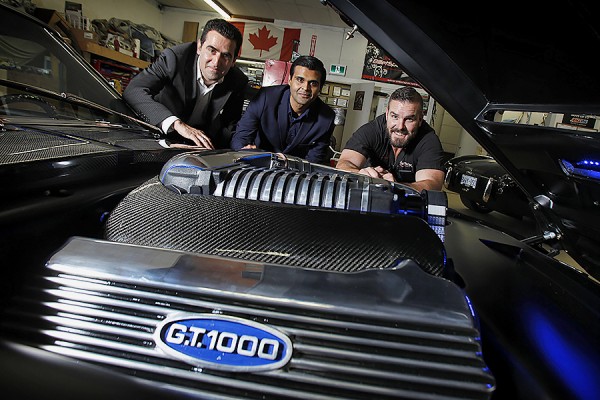
Not only were they the finishing touches, custom valve covers engineered by University of Windsor students were “one of the nicest touches” on a one-of-a-kind Mustang custom-built by a local auto shop.
“On a car that’s extremely beautiful front to back, the engine compartment we worked on with the university is now the sharpest part of the car,” says Chris Darmon, one of the owners of Xcentrick AutoSports, a shop in Oldcastle that specializes in classic and custom cars for a local and global market.
Darmon said they usually do everything in-house, but they needed outside help to bring to life a Toronto customer’s vision for his 1967 GT500 Mustang.
“The customer wanted the valve cover on a 2014 Ford Coyote 5.0L V8 engine to look like a 1960s design,” said Saad Zafar (BASc 2011), who was introduced to Darmon through the university’s EPICentre. “There was nothing like that on the market, so we had to start from scratch.”
Zafar started working on the project when he ran a 3D printing start-up through the EPICentre. After the start-up folded, Zafar — who now works as a continuous improvement engineer at Catalent, a pharmaceutical manufacturer in Windsor — enlisted the help of Hamed Kalami, a PhD student at UWindsor who specializes in reverse engineering, product design and modeling.
“We bounced our ideas back and forth,” Darmon said. “I sent them some pictures to show them what I was envisioning for it and they put pen to paper and came up with the design.”
The two started by reverse-engineering the existing valve cover then used a 3D printer in professor Jill Urbanic’s lab to create prototypes.
“That was the most crucial part, that we were able to print some prototypes before we actually manufactured the real part,” said Zafar, a car lover who chose to attend UWindsor for its strong ties to the automotive industry. “The contours of the valve cover had to perfectly match the contours of the engine.”
Zafar and Kalami originally planned on making the covers out of plastic, but found the heat from the engine caused too much expansion and contraction.
“We ended up having to go to a machine shop to get it made out of billet aluminum so that it could withstand the power of the motor and the heat,” Darmon said.
Now that they were using aluminum, Kalami said minimizing the weight of the covers was critical to avoid vibration on the road. The students paid the shop multiple visits to ensure their measurements were accurate and that the valve cover did not interfere with any engine peripherals. Once all parties were satisfied with the design, the covers were machined at Omni Tool, a manufacturer in Tecumseh.
“There’s nothing like this on the market,” Zafar said about the vintage finned design. “That was another factor that pushed me and Hamed — that if we make it, this would be the first time ever someone has done something like this.”
Darmon said the car — one of the most sought after Mustangs in the world — will most likely be featured in magazines and car shows across North America. Over a three-year period, the Xcentrick team has put more than 6,500 hours in the car, which they’ve coined the GT 1,000 because of its 1,000-horsepower engine. The carbon fiber car can do an eight second quarter mile and can reach close to 400km with the air conditioning and radio on. Darmon said they even had to add a skeletal chassis underneath the vehicle to handle the muscle car’s power.
“Nobody usually goes to the extent we did with this car,” Darmon said. “We’ve touched every square inch of this car. Even a non-car person can appreciate the beauty.”
Going forward, Zafar, Kalami, and Dr. Urbanic plan to research and experiment with sand casting using modular 3D printed patterns to manufacture customized, made-to-order valve covers.
“Our group has the potential to design and make any customized valve cover or even other cosmetic parts of a car,” Kalami added.